Continuous machine monitoring and diagnosis in one tool! One enabler is our own hardware mmBox and sensors from selected third parties. But we can also process data from existing installations: a REST API interface enables users to send machine data for analysis and get the results or Dashboard content back (e.g. via MQTT). Our system is based on novel and patented data processing of sensor data of any kind using machine learning and AI methods, see Downloads. We differentiate ourselves from MEMS-based IoT systems through:
Increased plant availability
through early damage detection
Do you wait already months for spare bearings? Is your plant at a standstill due to an unexpected breakdown? Possibly even at a critical moment when you would need to rely on full capacity? Most of such interruptions can be avoided. By switching from condition-based to predictive maintenance, you determine the timing of maintenance and repair of your system yourself. We make your machine transparent!
Diagnosis-as-a-Service (DaaS)
- Save an consultant: 24/7 diagnosis for the price of an annual inspection
- Highly sensitive, very low noise floor, suited for slow runners!
- We see far ahead
- We see any detail thanks to its high resolution
- Unique trend charts and automatic diagnosis
- Click & Run - automated monitoring and alarm threshold setting
- Anomaly detection – early bearing and gear defect identification
- Safe and reliable - system architecture which manages machine data and metadata separately
- Independent and transparent - no hidden costs to get access to your data, no affiliation to any third party
- Access independent of location, time or device (BYOD), system can be added at any later date
- Intuitive results and user friendly – results and graphs interpretable by anyone
Maintenance 4.0 and everything is under control
- Monitoring of critical bearings or gearboxes
- Detection of incipient failures - due to small deviations from the standard
- Scheduling of maintenance work and repairs
- Optimize plant utilisation
- Avoid unplanned interruptions during operation
Our solution consists of a well-rehearsed and proven system of sensors, best-in-class data acquisition and novel data processing, paired with an evaluation individually tailored to your plant and needs. This allows you to optimally plan maintenance and repairs.
Optimize plant availability
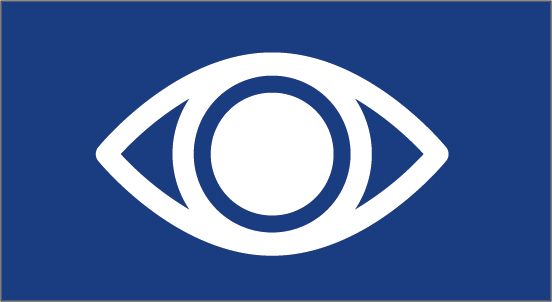

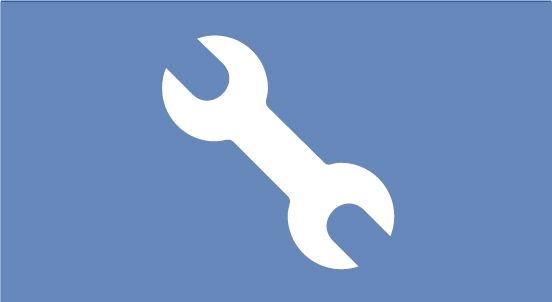
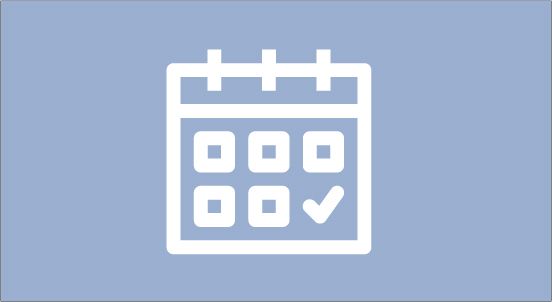
Repair & maintenance planning
Mechmine leads the way
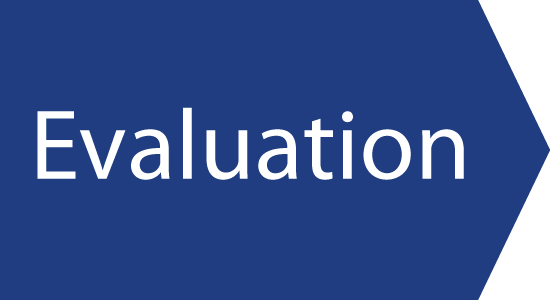
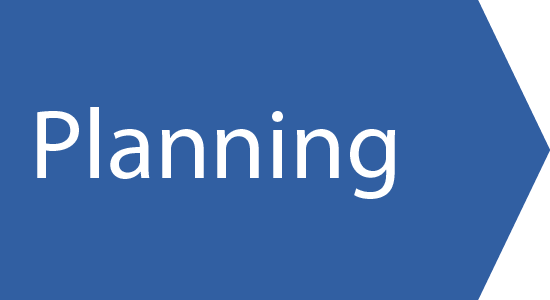
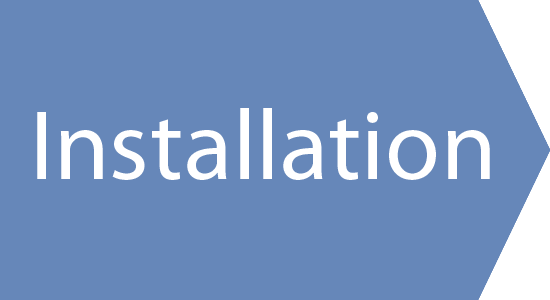
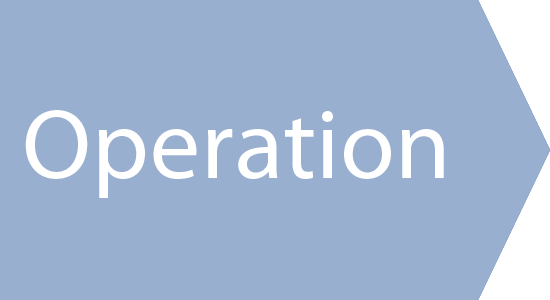
Customer testimonials - Mechmine technology convinces
Our preventive maintenance solution is already successfully in use in many places.
Further references:
- Swiss Railways SBB
- Bayer AG
- SEW
- Schindler AG
- Amt für Industrielle Betriebe Baselland
- Funicular railways
- Hydropower plants
- Watertreatment plants
You can find more examples under references.
News
Mechmine at the IFAT trade fair in Munich!
Munich is not only home to wheatbeer and pork-knuckles, but also the world's leading trade fair for water, sewage, waste and raw materials management. A visit is all the more worthwhile!
Mechmine and Yazzoom cooperate
Mechmine and Yazzoom announced that they have entered into a partnership agreement to offer together a broad portfolio of advanced predictive maintenance solutions to the market. The combined offer of Mechmine and Yazzoom is suited for a broader range of predictive maintenance challenges.
Imbalance-Alignment-Looseness Tool
Machine errors like imbalance, misalignment or looseness account for the majority of issues in rotating machines. Therefore, their fully automated identification is of high relevance and...
You will meet us at the following events
Our system
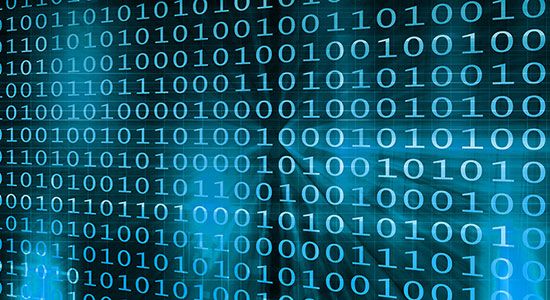
Massive improvement in performance
mechmine - data mining searches for the right information
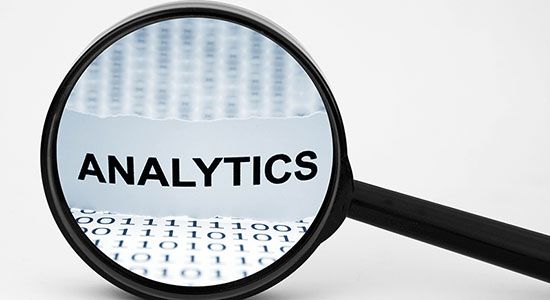
Everywhere - Anytime - Everything
mechmine - Platform-as-a-Service (PaaS)
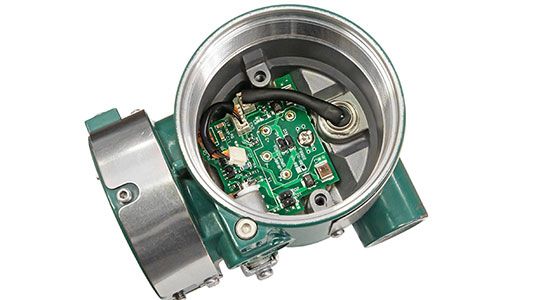
Mechmine utilises the latest technologies
mechmine - sensors are our data sources
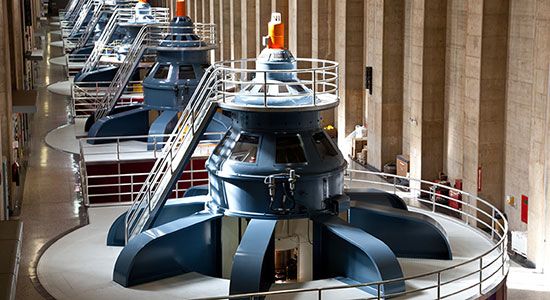
We prevent machine failures
mechmine - monitors machine vibrations
Mechmine technologies in action
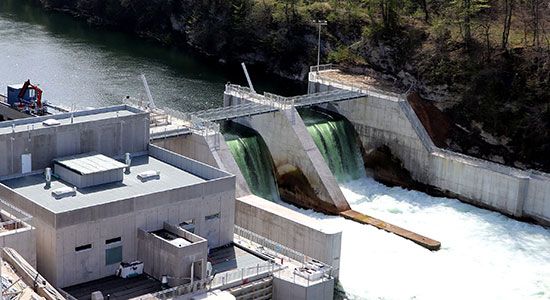
hydro power plants
Monitor the health of bearings and gearboxes of critical plants successfully. Mechmine offers a secure and powerful solution.
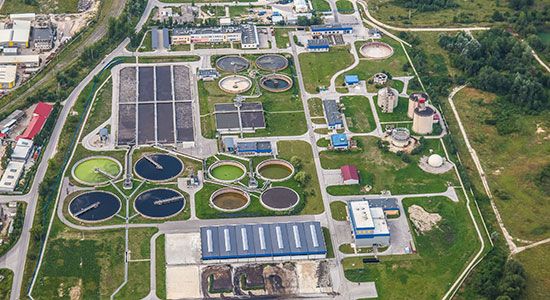
water treatment plants
Water treatment plants use redundancy to increase plant availability, specifically process continuation, which is costly and space demanding.
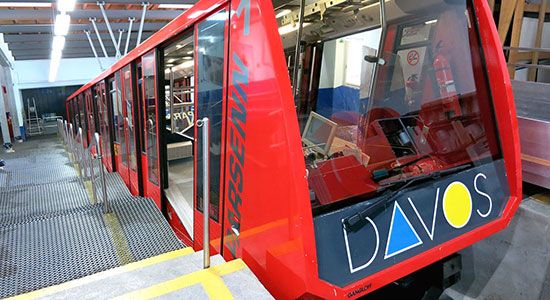
mountain rails and lifts
Early detection of anomalies, mobile access to data due to cloud-based machine monitoring.
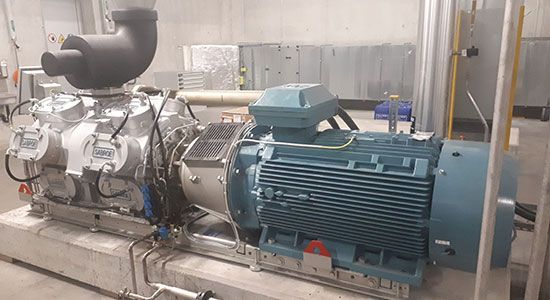