Knowing bearings’ Remaining-Useful-Life (RUL) is of great value to machine operators. Mechmine commissioned a high-performance RUL testbench to speed-up their ongoing effort to calibrate their algorithms.
A 1.2 ton high-precision testbench with 10 industry-grade bearings like 6319C3 has been put in operation, see image below. The shaft is powered by a 5.5kW frequency-controlled motor (Optidrive™) with separate fan.
In the coming weeks, Mechmine will monitor the life cycle of bearings while they age until failure. To accelerate the process of developing defects, each bearing can be stressed individually through, for example, a point-force on the bearing’s outer ring. Today, Mechmine has more than 11’000 real-world datasets from 123 bearings, each with duration of multiple seconds. Of course one could chop each dataset into multiple shorter pieces to obtain more datasets. But experience showed that this impacts performance. More important is to observe bearing failures in industry deployed motors but this takes time as they occur infrequently. Thus Mechmine can increase its data portfolio quicker by collecting real (RUL) data with the testbench. This allows Mechmine to optimise their RUL prediction and bearing-defect detection algorithms.
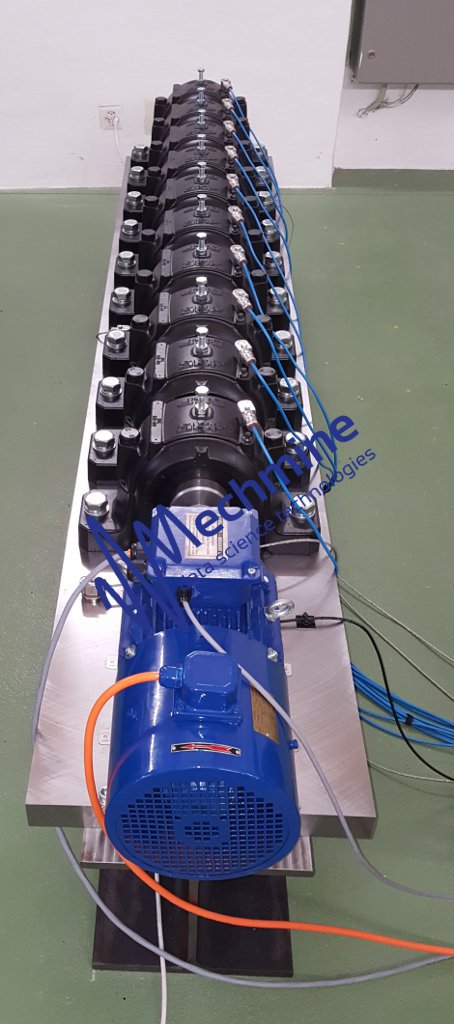